Fungování podnikového IT se mění - z modelu následování požadavků se přechází na model spolupráce. "Inovacím se nedaří ve striktně hierarchických organizačních strukturách, proto jsme zavedli multifunkční kompetenční sítě jdoucí napříč celým podnikem a tvořící základ AIR center (Audi Innovation Research) v San Francisku, Pekingu a několika německých lokalitách, kde si pracovníci z různých firemních a IT oddělení vyměňují názory na další směřování společnosti ve světě nových technologií," říká Mattias Ulbrich, data manager ze společnosti Audi pro Digital McKinsey.
Audi dosahuje na poli digitalizace výrobních procesů významných úspěchů. Jenom namátkou - komplexní digitální monitoring vozidel procházejících výrobní linkou nebo in-line řízení kvality, kdy kvalita je operátory na montážních linkách řízena přímo, a ne ve speciálních kroužcích kvality, jak je v branži obvyklé.
Automobilka se netají výraznými nárůsty v oblasti produktivity výroby, kvality produktů a procesů a v neposlední řadě i logistiky.
Modernizují také dodavatelé pro automotive
"Historicky se výrobní týmy vždy nějak snažily vyjít s IT. Musíme se však naučit opravdu spolupracovat, i když to znamená změnu dosavadního způsobu práce," zmiňuje Justin Hester, výzkumník z laboratoří Hirotec Group, jednoho z největších světových dodavatelů dílů pro automobilový průmysl.
V této společnosti zapojili Průmysl 4.0 do snížení neplánovaných zastavení výrobních linek.
"V našem odvětví platí, že výpadek linky stojí dodavatele v Severní Americe 1,3 mil. dolarů za hodinu, tj. 361 dolarů za vteřinu. Pokud někam voláte tři minuty pro nahlášení chyby, tak jste právě přišli o 70 tisíc dolarů jenom proto, abyste ohlásili, že máte problém. Zastavení linky se u klíčových procesů může rovnat zastavení zákazníka, tedy ukončení kontraktu," dodává Hester. Za tímto účelem japonský dodavatel spároval platformu internetu věcí PTC společnosti Hewlett Packard Enterprise se systémy HPE Edgeline, čímž významně posílil možnosti propojení výrobních operačních technologií s prediktivní analytikou.
Očekávané přínosy Průmyslu 4.0 z pohledu amerických výrobců
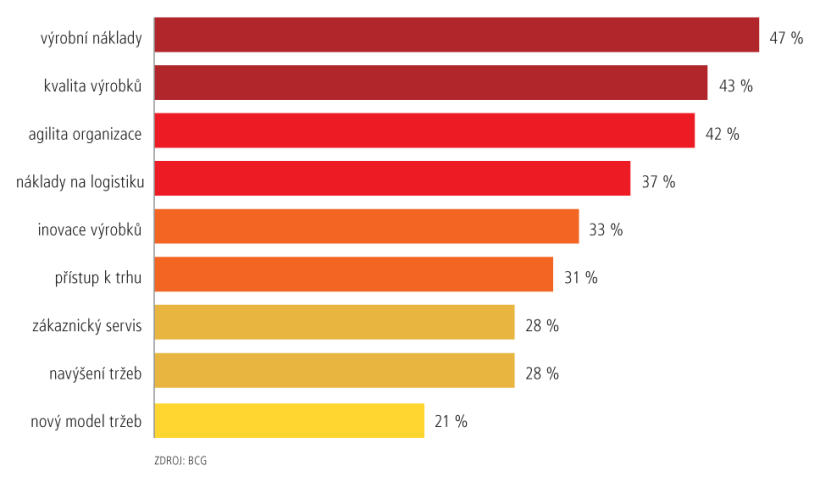
Na této platformě zrealizoval Hirotec ve svých továrnách tři pilotní projekty. První z nich v Detroitu, kde monitoruje a analyzuje data z osmi CNC strojů. V dalším se zaměřují na dálkovou vizualizaci automatické inspekční linky výfukového systému. Zdroje dat zde zahrnují inspekční roboty, silové senzory, laserová měřicí zařízení a kamery. Ve třetím pilotu testují vizualizaci celé výrobní linky v reálném čase a automatickou generaci zpráv ve výrobně automobilových dveří.
Prostřednictvím pilotních projektů získal Hirotec přehled o výrobních operacích v reálném čase, což společnosti umožňuje okamžité řešení problémů, jež přímo ovlivňují propustnost a výkonnost výroby. Řešení též umožňuje využití strojového učení pro předvídání a prevenci poruch v kritických systémech, jakými jsou například kontrolní linky u výfukových systémů.
Pohled McKinsey
Ve svém reportu Jak navigovat digitalizaci ve výrobním sektoru z roku 2015 hodnotí poradci McKinsey hlavní páky digitalizace z již realizovaných projektů digitálních továren takto:
- zvýšení procesní produktivity o 3 až 5 procent,
- snížení výpadků strojů o 30 až 50 procent,
- zvýšení produktivity práce u technických profesí o 45 až 55 procent přes automatizaci,
- pokles nákladů na držení zásob o 20 až 50 procent,
- redukce nákladů na kvalitu o 10 až 20 procent,
- přesnost forecastingu 85+ procent,
- zrychlení přístupu k trhu o 20 až 50 procent,
- snížení nákladů na údržbu o 10 až 40 procent.
Ve svém loňském reportu Digital Manufacturing Global Expert Survey tým McKinsey zpovídal 400 zástupců výrobců a jejich dodavatelů ze čtyř klíčových trhů - Spojených států, Německa, Japonska a Číny. Dospěli přitom k názoru, že trend Průmyslu 4.0 je novým významným zdrojem růstu produktivity, přičemž pokrývá vzrušující řadu digitálních technologií, jež jsou nastaveny na dosud nepoznanou změnu zažitých průmyslových, ale i obchodních postupů. Zatímco na Zemi je dnes propojená asi miliarda lidí, navzájem zesíťovaných strojů už je zhruba 50 miliard.
Podle průzkumu přinese vlna Průmyslu 4.0 pokrok v mnoha oblastech do každého z průmyslových odvětví.
Polovodiče
- Automatizovaný dispečink v reálném čase zajistí až 90 procent úspory operátorů při navýšení produkce o 30 až 50 procent.
Automobilový průmysl
- Implementace datové analytiky v reálném čase sníží prostoje strojů a zredukuje náklady na řízení kvality o 20 až 30 procent.
Letecký průmysl
- Pokročilá analýza poptávky po leteckých komponentech má zkrátit cyklus uzavírání dlouhodobých smluv (LTA) o čtyři týdny při současném zvýšení tržeb o 2 až 3 procenta.
Spotřební průmysl
- Zavedení inteligentního zásobování (smart inventory) a automatického objednávání sníží náklady na řízení zásob o 20 až 50 procent.
Důlní průmysl (uhlí a nerosty)
- Pokročilá analytika dokáže zvýšit výtěžnost až o 3 procenta.
Těžařský průmysl (ropa a plyn)
- Digitalizace ropných vrtů umožňuje zlepšit plánování lidských zdrojů, vlastního vývoje a provozu v terénu v rozmezí 30 až 50 procent.
Energetika
- Pomocí prediktivní údržby zde může docházet k úsporám až ve výši 45 procent.
Jak to vidí BCG
Z průzkumu, který provedla firma Boston Consulting Group mezi 380 manažery amerických výrobních podniků vyplývá, že vidí největší možné přínosy Průmyslu 4.0 v nárůstu produktivity (89 procent) a snížení výrobních nákladů (47 procent), méně ale už třeba v nárůstu tržeb (28 procent). Jak je zřejmé z grafu, po redukci nákladů největší očekávání vzbuzuje zvyšování kvality výrobků (43 procent) a agilita vnitropodnikových operací (43 procent). Ještě menší naděje než do navýšení tržeb vkládají lídři amerického průmyslu do vzniku nových byznysových, potažmo tržních modelů (13 procent). Konzultanti BCG k tomu poznamenávají, že stejná očekávání, jaká vyvolávají úspory nákladů, by u amerických výrobců měly vyvolávat i nárůsty tržeb.
BCG dále uvádí devět klíčových technologií, jež sehrají hlavní roli v transformaci příští výroby. Je zajímavé, že na tomto seznamu nefiguruje dnes všude skloňovaná umělá inteligence.
Coboti - snadno programovatelní a s člověkem spolupracující roboti s integrovanými senzory a standardním rozhraním pro styk s okolním světem.
89 %
Takové procento manažerů vidí největší možné přínosy Průmyslu 4.0 v nárůstu produktivity. Vyplývá to z průzkumu, který provedla firma Boston Consulting Group mezi 380 manažery amerických výrobních podniků.
Aditivní výroba - 3D tiskárny zaměřené na výrobu náhradních dílů a funkčních prototypů. Vhodně decentralizovaná 3D pracoviště šetří náklady na dopravu a zásobování.
Rozšířená realita (AR) - digitalizace pracovního prostředí s plnou podporou zobrazovacích zařízení, např. brýlí. AR výrazně zlepšuje standardní pracovní postupy (SOP), údržbu a logistické procesy.
Simulace - simulační technologie typu digitálních dvojčat představují virtuální reprezentaci reálných fyzických objektů, procesů a systémů umožňující jejich optimalizaci před vlastním uvedením do ostrého provozu.
Horizontální a vertikální systémová integrace - integrace dat napříč celým podnikem s podporou standardních protokolů přenosu dat představuje plně integrovaný hodnotový řetězec (od dodavatelů až k zákazníkům) i organizační strukturu (od výrobních linek až k vedení podniku).
Industriální IoT - komplexní zasíťování výrobních zařízení, linek a produktů, vícesměrná komunikace propojených objektů.
Cloud computing - správa a řízení obrovského množství dat z otevřených systémů, vícesměrná komunikace výrobních systémů a zařízení v reálném čase.
Kyberbezpečnost - správa a řízení zvýšeného bezpečnostního rizika z důvodu vysoké úrovně propojení inteligentních zařízení, produktů a systémů.
Big data a analytika - komplexní zpracování a vyhodnocení dostupných dat z podnikových systémů s podporou rozhodování v reálném čase.
PwC a data z Německa
Další průzkum z oblasti Průmyslu 4.0 zpracovali v loňském roce pod názvem Digitální fabriky 2020 konzultanti PwC na vzorku 200 vrcholových manažerů německých průmyslových podniků.
Manažeři od našich sousedů nahlížejí na investice do Průmyslu 4.0 jako na strategické s delší dobou návratnosti - a to v průběhu tří až pěti let. V tomto období očekává celých 98 % respondentů studie zvýšení podnikové efektivity o 12 procent.
Hybatelem digitální transformace podniku musí být topmanagement a začít by měl okamžitě. Implementace digitální výroby znamená budování digitální pracovní síly. Podniky jsou schopné činit chytřejší rozhodnutí na základě prediktivních analýz a strojového učení. Technologie typu cobotů, digitálních dvojčat či rozšířené reality vedou ke štíhlejším a progresivnějším výrobním postupům. Základem k tomu je dle průzkumu propojování výrobních lokalit (interních i externích) prostřednictvím integrovaných výrobních informačních systémů MES.
Ve zvýšení produktivity u digitálních továren věří, jak již bylo zmíněno, 98 procent manažerů. Co je ale rovněž pozoruhodné, je jejich náhled na lokální, resp. regionální budování chytrých továren. Tři čtvrtiny dotázaných vedoucích pracovníků německých podniků se domnívají, že lokální digitální továrna je mnohem efektivnější než offshore fabriky v zahraničí. Ta může na požadavky zákazníků reagovat mnohem pružněji, rychleji a s daleko větší dynamikou.
Očekávané přínosy Průmyslu 4.0 z pohledu amerických výrobců
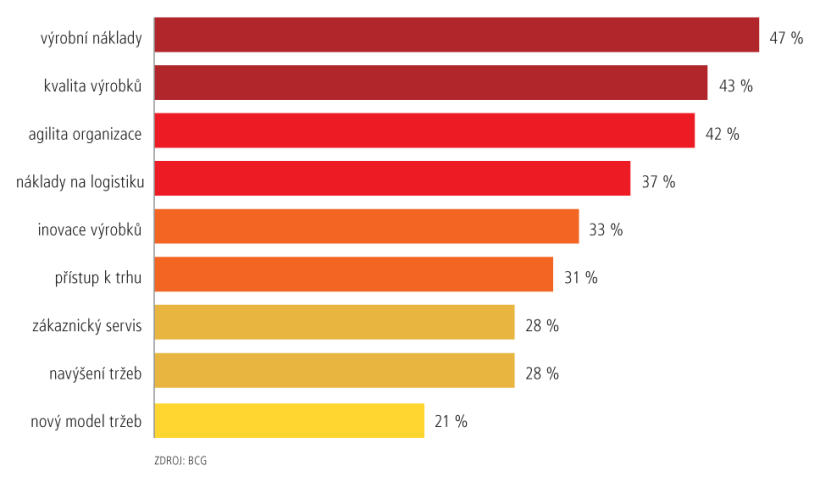
Přidejte si Hospodářské noviny
mezi své oblíbené tituly
na Google zprávách.
Tento článek máteje zdarma. Když si předplatíte HN, budete moci číst všechny naše články nejen na vašem aktuálním připojení. Vaše předplatné brzy skončí. Předplaťte si HN a můžete i nadále číst všechny naše články. Nyní první 2 měsíce jen za 40 Kč.
- Veškerý obsah HN.cz
- Možnost kdykoliv zrušit
- Odemykejte obsah pro přátele
- Ukládejte si články na později
- Všechny články v audioverzi + playlist